Roller-Compacted Concrete
- Ir Teng Keat Hui, Mike
- May 19, 2018
- 2 min read

Roller-compacted concrete (RCC) is designed to resist the force applied by external compaction equipment. It may or may not contain supplementary cementing materials. The mix is stiff being dry and lean with zero slump. It has the consistency of damp gravel. With a low water content, it needs to be mixed in a continuous flow system (normally in a pug mill mixer).
It can then be spread with a modified asphalt paver and compacted with a roller.

This process will produce the required strength and characteristics of conventional concrete.
A pug mill plant is normally set up on site to enable continuous flow of materials to achieve the desired productivity. They can either be of mobile type:
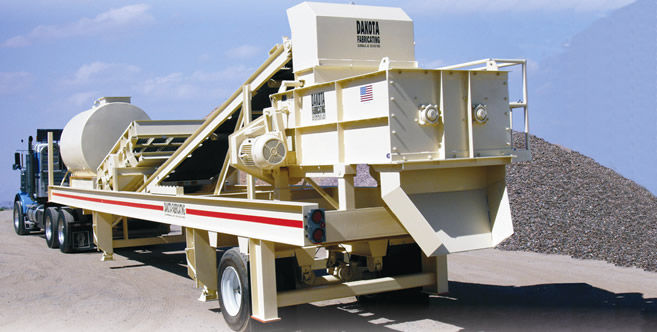
or those of easily-transported type:
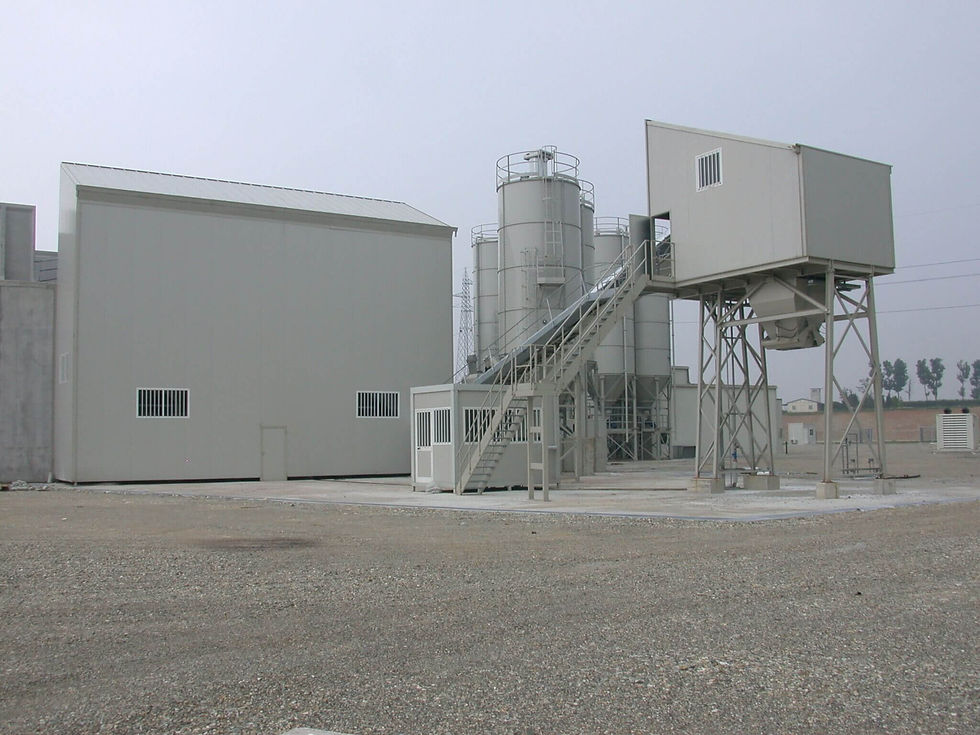
The pug mill provides a vigorous mixing action which is necessary to disperse teh small amount of mixing water throughout the RCC.
The whole process does not require any formwork, finishing, surface texturing or joint sawing and sealing. RCC requires only about 60-70% of cement compared to conventional concrete. This reduces heat of hydration typical of mass concrete.
Water content is so low the freshly mixed RCC resembles damp gravel. Where site condition allows, it can even be transported in dump trucks or paver or loaders.

It can also be spread with bulldozers or conventional asphalt spreaders or graders in 200-300 mm thick layers, called lifts.

Lifts are then compacted by using vibratory steel-wheel and pneumatic tyre rollers to 95-100% of the specified density.

Immediately after compaction, water is sprayed as a fine mist to cure the concrete.

Since RCC can be sized and shaped with conventional paving machines, it is often used in the construction of gravity dams by using methods and equipment similar to those used for earth dams. By using RCC, labour use is redued drastically.

The main challenge in using RCC is to obtain sufficient bond between lifts. This challenge is more profound in drier consistency of RCC mix, particularly mixtures containing aggregates larger than 40 mm nominal size. Bond can be improved by restricting the time interval between lifts or by providing supplemental joint treatment. An alternative would be to increase the paste content of the mix.
Comments